Manufacturing facilities owner
Transforming Internal Application Into Revenue Opportunities
The client wanted to generate a new revenue stream by going to market with a solution born from an internal application.
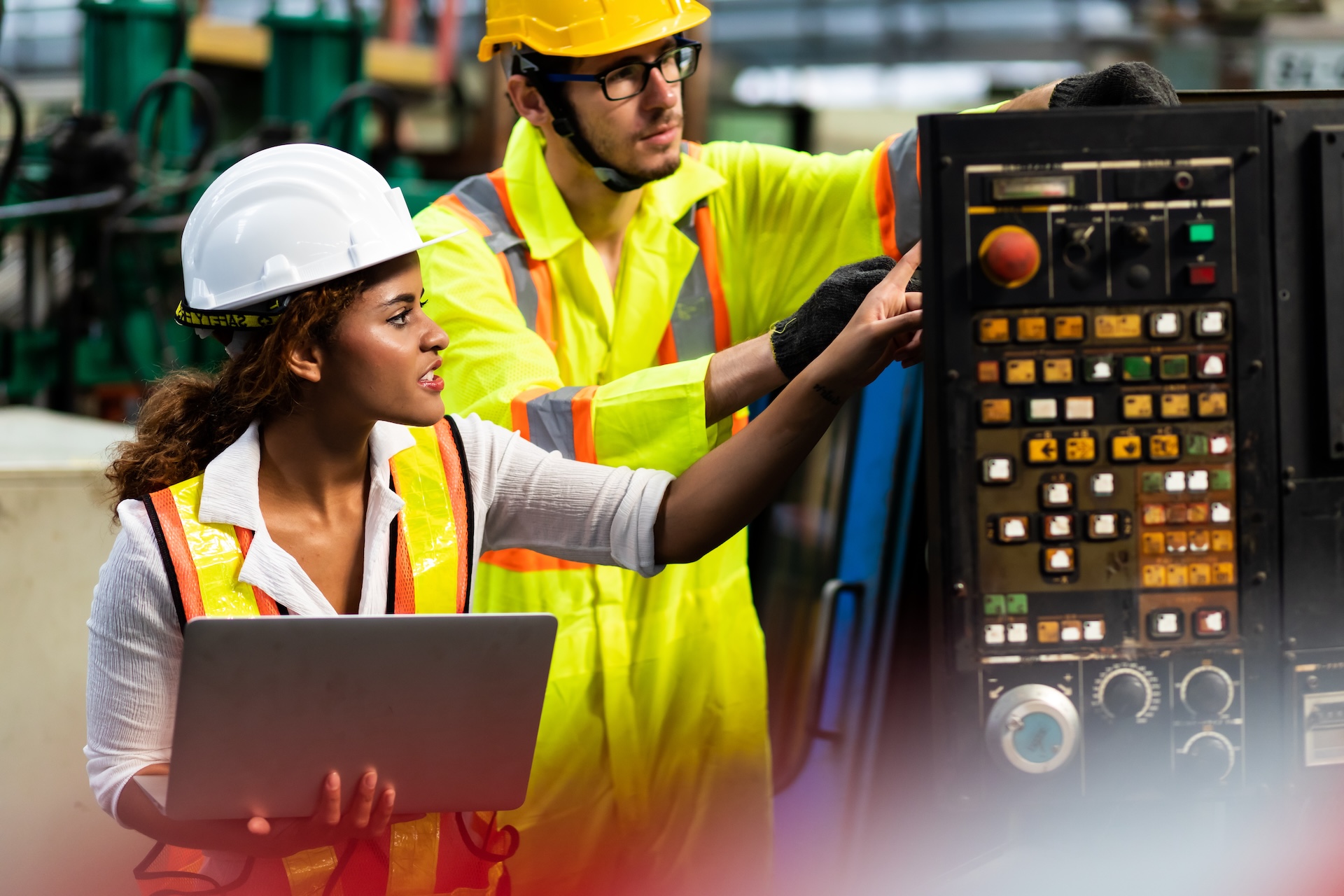
key deliverables
tools & technologies
The Challenge
Go to Market with Assembly Line Process Software
Customers sometimes help businesses launch new products, and that’s exactly what happened during tours of one of our clients’ manufacturing facilities. Customers kept commenting on just how impressed they were with the custom software used to manage the assembly production line. Several felt the application could help other manufacturing companies run their processes more efficiently as well.
The company’s senior leadership team had long recognized the value of the assembly line process software and took these customer suggestions to heart. They decided to launch a new product to bring the solution to market. To ensure the success of the new endeavor, the leadership team also decided to update the legacy application and offer it as a software-as-a-service (SaaS) subscription.
Before going to market, we wanted to make some improvements to the software and test those changes internally. In addition to giving us a more robust solution to offer to customers, the enhancements would help us improve the flow of our internal assembly line processes.
IT Director
One of the key new capabilities they wanted to add was a dashboard to generate real-time visibility into assembly line performance and product quality. This would make it possible to identify production flow issues during production runs—rather than waiting for nighttime reports and quality assurance checks at the end of runs.
The legacy version also required manual intervention to refresh the dashboard’s data, and the refresh process required an extended time frame. Finding issues sooner in the process—such as a defective component or an assembly step creating a bottleneck—would allow for earlier modifications to the flow. And adjusting in real time is less costly than making alterations at the end of a production run.
The Solution
Allata Helps Accelerates Go-to-Market Timeframe
The client wanted to go to market quickly to unveil its process for managing assembly lines more efficiently before a competitor beat them to the punch. But to meet that target, they IT director realized the company’s internal software development resources did not have sufficient bandwidth and experience in newer technologies such as React, Node.js, and AWS serverless. To update the legacy assembly line application and to add the dashboard on time, they decided to turn to an outside software development partner.
A colleague from another company strongly recommended they consider collaborating with Allata, who they quickly recognized would be an ideal partner.
In addition to providing strong software coding and development process capabilities, Allata understands the manufacturing industry. They also invest time to delve into how a customer’s particular processes run. This makes it a lot easier for us to communicate what we need and for Allata to hit the ground running.
IT Director
The client valued that Allata offered software developers who were well versed both back-end and front-end coding along with the ability to design and implement cloud-native applications that are cost-optimized from the ground up. Allata also provides project managers who can advise on implementing development processes that help software projects progress continuously. For them, Allata deployed a combination of Agile, Kanban, DevOps and CI/CD methodologies.
The communication skills Allata brings to the table also make it easier for internal development teams to work with an external partner. This was particularly important for our client in helping internal resources adopt a more formal software development process.
The Results
Assembly Line Flows More Smoothly
The Allata team first focused on improving the dashboard that the client required for real-time views into the flow and the product quality of its assembly line process. The dashboard gives managers the ability to easily change sorting and grouping views and automatically updates in near real-time. Production line operators just fire up the dashboard in a monitor above the production line with no need to plug in a mouse or keyboard. There’s also no need to manually refresh the data.
If an issue occurs, it allows users to record it while the dashboard displays it in real time. This enables line leads and supervisors to inspect issues instantly and take action within minutes. Managers can also access reports that are generated instantly based on the available data.
With immediate quality feedback for any production issues, the client can now catch problems in the middle of the process rather than during QA, when it’s costlier to make product adjustments. With bottlenecks removed immediately, they also benefits from improved operational efficiencies and increased output—with products flowing more smoothly through the production process.
Efficient assembly is all about establishing a smooth flow and keeping the line moving at a consistent pace. And that’s where the dashboard that Allata devised for us helps. We may adjust up and down depending on how much volume we want to produce in a given day, but we need to make sure the tasks at each stage are evenly distributed to keep things moving smoothly.
IT Director
After developing the dashboard, Allata then began helping the client’s internal development team with enhancements to the base assembly line management application. Allata also added controls to improve the security posture of the application. In the future, they believe may turn to Allata for help with technical support as customers start using the application.
With the help of Allata, the client is now on the brink of a new revenue-generation opportunity. In addition to manufacturers with assembly lines, the solution can assist companies that need to improve the efficiency of any process flow. The software can take any set of instructions and break down the processes to make sure they flow smoothly.
Every member of the Allata team is a professional and easy to work with. They are open to suggestions and very flexible in the way they work with our internal team. We expect Allata to continue to play a major role in our success.
Manufacturing client
Innovation starts with a conversation.
Fill out this email form and we’ll connect you with the right person for your needs.
Related Case Studies
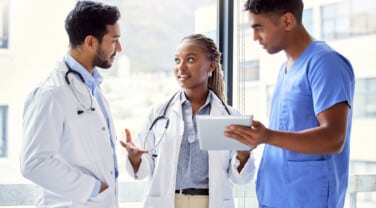
Healthcare Staffing Leader Establishes Integration Center of Excellence to Accelerate Digital Transformation
- Healthcare & Life Sciences
- Technology & Cloud
Healthcare & Life Sciences, Technology & Cloud
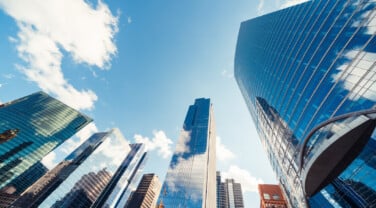
Leading Real Estate Firm Streamlines European Operations with Unified Property Management Platform
- Real Estate & Construction
- Technology & Cloud
Real Estate & Construction, Technology & Cloud
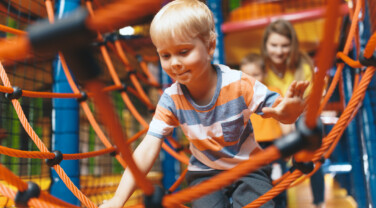
From 15 Minutes to 2 while saving $750,000 per year: Revolutionizing Urban Air with an AI-Driven Custom POS.
- Travel Hospitality and Entertainment
- Technology & Cloud
Travel Hospitality and Entertainment, Technology & Cloud